Factory Address
P-Plus Sdn Bhd
No. 5, Lorong Industri 13,
Kawasan Industri Bukit Panchor,
14300 Nibong tebal,
Penang, Malaysia
Tel:+604-593 8971 Fax:+604-5938 975
Overview
Engineering
Manufacturing
P-Plus Sdn Bhd
No. 5, Lorong Industri 13,
Kawasan Industri Bukit Panchor,
14300 Nibong tebal,
Penang, Malaysia
Tel:+604-593 8971 Fax:+604-5938 975
Service Center
+604-593 8971
+604-593 8971
Engineering Overview
Component Engineering
- A big part of cost in electronic products arises from the types of components used. Lead times, stocks availability, customizations, and manufacturer’s minimum order quantities can quickly hike up the total cost of materials. As customers identify the Bill of Materials and manufacturer’s part numbers, we can propose alternative components that can bring down the total cost of product down over time.
New Product Introduction (NPI)
- We provide customers with early program life cycle support to meet your costing and lead time. A successful NPI requires integration of product design and the processes has to be aligned to your business and product strategy. With our set up, we provide experienced prototyping and product development services from NPI to volume manufacturing.
-
Our benefits include:
- On site prototyping, low to medium volume manufacturing
- On site engineering, manufacturing, testing and supply chain support
- DFM, DFT and cost optimization
- Component engineering. BOM Analysis
- Prototype PCB fabrication, assembly, testing and validation
- Cable, enclosure design and fabrication
- Reliability test and analysis
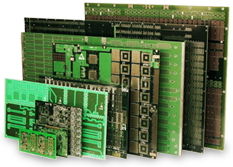
DFM
-
Design for Manufacturability (also sometimes known as Design for Manufacturing)- (DFM) is the general engineering art of designing products in such a way that they are easy to manufacture. The basic idea exists in almost all engineering disciplines, but of course the details differ widely depending on the manufacturing technology. This design practice not only focuses on the design aspect of a part but also on the producibility. In simple language it means relative ease to manufacture a product, part or assembly.